24 Hour Breakdown Service
Food Production Engineering Services
Mechsol have extensive experience in supporting food producers throughout London and the Southeast. Our specialist food production engineering services include servicing, repairs, line optimisation and 24hr emergency breakdown response. Our priority is to maximise our customers productivity while providing impeccable customer service.
Food Production Machinery Servicing and Maintenance
Our food production machinery maintenance service is designed to maximise production uptime and minimise costly breakdowns. With over 15 years’ experience working with food companies, we have extensive expertise covering a wide variety of food processing equipment and packaging machines. We are also fully conversant with the requirements for working in “clean room” and hygiene critical environments. Examples of food production machinery we maintain are:
- Flow wrappers
- VFFS Baggers
- Tray sealers
- Shrink wrappers
- Slicing machines
- Conveyor systems
- Large hoppers
- Filling machines
- Blade sharpening and grinding
- Stillage and skip repairs
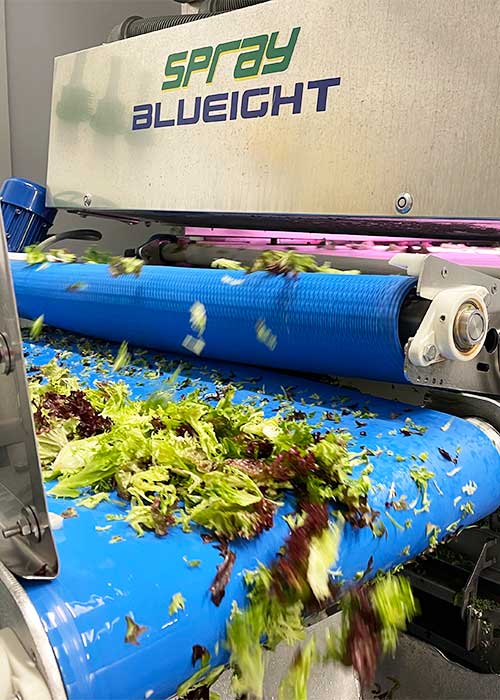
Our expert engineers have experience maintaining a huge variety of machinery, but we have specialist knowledge of brands including Ulma, Isheda, Omori, Turatti and Thilot. This means that we can often keep older machinery working by sourcing parts or having them specially made. Our engineers can also install a wide variety of new machinery, making alterations to framework and services where required. We can also help producers to cut costs with our production line optimisation service.
Individually Tailored Maintenance Contracts
No two producers are the same, for this reason our maintenance services are designed to cater for producers’ individual needs. We offer “one-off” service visits or planned maintenance contracts. All works are carried out by trained and experienced engineers at a time convenient to you, be that day, night, or weekends. Our flexible approach is designed to minimise disruption to production schedules and productivity.
Planned maintenance keeps your food production and packaging machinery in good condition, often identifying unseen issues before they become costly breakdowns. Our maintenance service begins with a full health check and visual inspection. Following this, we provide a report detailing all maintenance works, parts required and recommendations for repairs or upgrades. We can supply spare parts if required, or fit parts supplied by you. If you require on-time machine maintenance or would like to know more about our tailored service contracts, please do contact us.
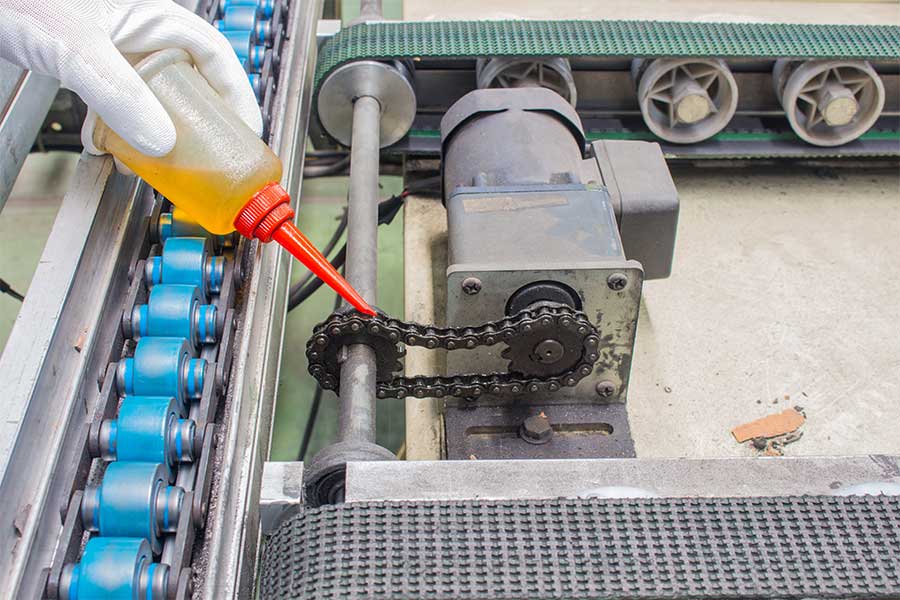